Stock Turns What it is?
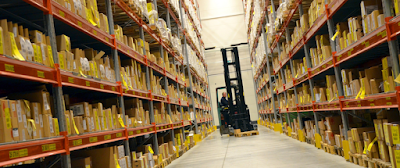
Stock Turns What it is? Stock turnover is a measure of operational efficiency. Specifically, it tells you how many times stock or inventory is being sold and purchased over a given time period. A low turnover rate may point to overstocking, obsolescence, or deficiencies in the product line or marketing effort. A high turnover rate may indicate inadequate inventory levels, which may lead to a loss in business. For example, a supermarket sells fast moving consumer goods so the stock turnover will be higher (say) 50; whereas a white-ware Retailer would have a lower turnover of (say) 6. In manufacturing, a reasonable Stock Turn would be 8. The organization should compare industry's stock turns against other similar industries to determine a realistic value. If that cannot be done then simply improve the own Stock Turns to make it as effective as possible. Stock Turns are calculated in a variety of ways. However, one of the most common ways is to divide total sales CO