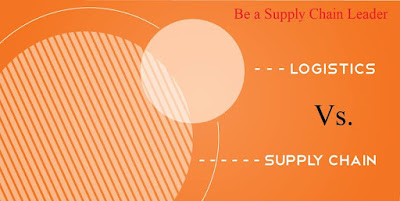
Difference Between Logistics and Supply Chain Management All the activities, associated with the sourcing, procurement, conversion and logistics management, comes under the supply chain management.Supply Chain Management, it is a broader term which refers to the connection, right from the suppliers to the ultimate consumer. Logistics Management is a small portion of Supply Chain Management that deals with the management of goods in an efficient way. Definition of Logistics Management The management process which integrates the movement of goods, services, information, and capital, right from the sourcing of raw material, till it reaches its end consumer is known as Logistics Management. The objective of this process is to provide the right product with the right quality at the right time in the right place at the right price to the ultimate customer. The logistic activities are divided into two broad categories they are: Inbound Logistics The activities which are c...